株式会社LINK-US
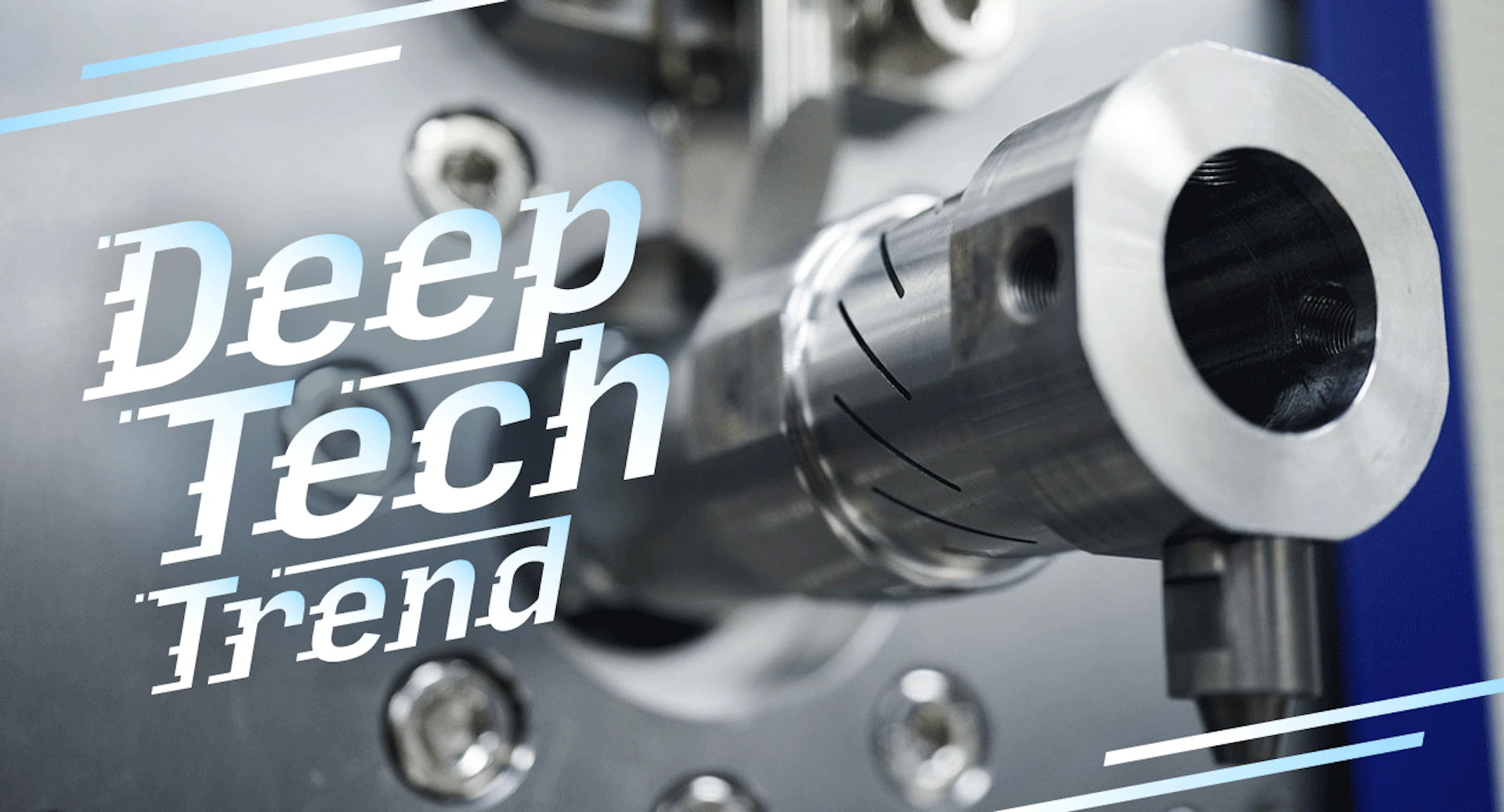
この企画では革新的な技術を持つスタートアップ企業を紹介していく。その技術がどのような背景から生まれ、どんな優位性を持っているか。社会に与えるインパクトを含めて解説する。
今回紹介するのは、世界的にもユニークな金属接合の特許技術を持つ株式会社LINK-US。同社の技術は、超音波振動によってハンダなどを必要とせずに金属をつなぎ合わせることができ、コストと時間を削減できるテクノロジーとして注目を集めている。電気自動車(EV)向けのリチウムイオン電池やパワーデバイスなどへのニーズも高まっており、海外大手企業との取引も進んでいるという。代表取締役の光行 潤氏に詳しく話を聞いた。
「円形の超音波振動で金属をつなぐ」世界で唯一の特許技術
―― LINK-USの事業内容について教えてください。
光行氏:当社は、金属接合における特許技術を開発・提供しています。従来の金属接合は、地金を溶かして金属をつなぐ「溶接」と、ろう材などの材料を利用して接合する「ろう接」が主流でした。工業界で最も有名なのは溶接で、低温で接合できるレーザー溶接などが一般的です。また、ろう接のカテゴリーで有名なものには、ハンダ付けやろう付けがあります。
金属を溶かして接合する溶接に対して、当社の超音波接合は金属を溶かさず、超音波の振動によって材料同士を直接つなぐ方法になります。これは現在、新たな金属の接合方法として注目されています。超音波で金属を接合するメーカーは他にもありますが、当社は超音波の振動の動きを楕円もしくは円形にすることができる「超音波複合振動接合」の特許技術を持つ世界で唯一のメーカーです。
―― 特許技術の中身について詳しく教えてください。
他社は円形ではなく直線の振動技術を採用しています。直線的に振動を行ったり来たりさせる往復振動です。これは折り返し時に速度が一度ゼロになるため、そこで振動エネルギーが失われてしまいます。なおかつ、材料側の板へのダメージも非常に大きくなります。
それに対して当社の複合振動は、円形でぐるぐる回る形の振動を与えます。速度がゼロにならず、非常に効率よく低エネルギーかつ低ダメージで、高い強度でぴったり接合させることができます。
もの作りのキープロセスである金属接合に革新を
―― 「超音波複合振動接合」を事業化したきっかけは何でしょうか?
超音波複合振動技術を発明した、当社の取締役会長である神奈川大学名誉教授の辻野次郎丸博士とは、前職での業務を通じて今から10年ほど前に出会いました。
私は前職の総合加工メーカーで、上流工程からアッセンブリ(組み立て)まで一通り経験しました。もの作りにおいて一番難しく、かつ重要だと思ったのが金属の接合です。もの作りにおけるキープロセスである金属接合において、辻野の発明を世の中に出さなければもったいないと思い、起業に至りました。
当初は、装置のズレやバラツキがなく、安定して複合振動のパフォーマンスを出すことにとても苦労しました。お客様から複数台の注文があった時に、すべて同じようによい楕円の軌跡を描けるようにするまでに開発を重ねました。5年ほど前には超音波のプロフェッショナルである社員の入社もあり、バラツキのない製品の量産化ができるようになりました。
―― 「超音波複合振動接合」技術の強みについて教えてください。
複合振動には二つの大きな強みがあります。
超音波は非常に扱いづらいもので、特に直線振動では振動を増幅させるホーンという大きな部品を頻繁に交換する必要があります。多い場合は2000ショットに1回換えなければなりません。そのたびに製造ラインが数時間止まるため、2170円筒型Libなどの車載用リチウムイオン電池であれば数十万個生産できるだけの時間をロスしてしまいます。当社はこの交換を容易にできる、先端の部品だけを交換すればよい「先端ホーンチップ交換式」を採用し、交換に必要だった数時間をわずか1〜2分に短縮しました。
消耗部品の交換時間が大幅に短くなり生産稼働率が上がります。さらに摩耗の原因となる折り返しがなく消耗品自体が長持ちすることや、交換部品が小さいため価格が直線振動の機械の半分〜3分の1程度に抑えられることも、お客様に喜ばれています。
もう一つの強みは、飛散物の軽減です。溶接には飛散物(スパッタ)がつきもので、これが電池の内部で発生すると、異物混入となり場合によっては発火の原因となります。
超音波接合は金属を溶かさないため飛散物は出にくいです。ただ、直線振動は折り返しの部分で材料側に大きなダメージを与え、削り取られた金属が飛散物となってしまいます。その点、複合振動は折り返しがなく、少ないエネルギーで接合が可能なので、材料へのダメージを減らし飛散物を出さないようにできます。
―― 御社の持つ特許技術は特にどのような製品にニーズがありますか?
今、圧倒的に世の中でニーズが高まっているのは、車載を主とした電池です。当社も電池の接合のニーズが最も高く、次いでパワーデバイスです。EV化に伴って高性能化、精密化している半導体の領域ですね。
高精度な次世代パワーデバイスなどでは、ハンダが排除される傾向にあります。次世代の車載用パワーデバイスの主流になると言われているSiC※は、300度という高温下でもパフォーマンスを発揮できるのですが、そこに熱環境に弱いハンダは使えないからです。
※SiC:シリコンカーバイド。シリコン(Si)と炭素(C)との化合物半導体。
電池が燃える原因はスパッタや異物混入だと言われています。かつて、旅客機のバッテリーからの発煙や、スマートフォンの発火といった事故がありましたが、原因は直線振動による超音波接合と考えられています。ほかにも、レーザー溶接が原因の製品大量リコールなど、接合に起因する発火は非常に多くあります。当社の技術を使えば、より安全で、燃えない電池を作れる確率が高まると思います。
EV化に貢献できる技術を日本から世界へ
―― 現在、特に注力されている領域について教えてください。
超音波複合振動接合が最も適していると注目されているのが、低コストで安定性が高い円筒形バッテリーです。テスラを始め、BMW、GMなども、この電池を車載用電池として採用する動きがあります。
当社は設立時から協業している日本最大手のバッテリーメーカーと一緒に、細く長いホーンを開発し、すでに実用化しています。当社が独占的に実用化できたのは、複合振動には直線振動のような折り返しがないため、細長くても安定して接合が可能だからです。また、テスラなど自動車向けの新型車載用リチウムイオン電池である4680(直径46mm×長さ80mmの円筒形電池)向けとしても、当社の製品は非常に注目されていて、実用化に向けてメーカーと進めているところです。
また、2170(直径21mm×長さ70mm)という、さらに小さい電池の需要も高まっています。当社の唯一無二の技術は、すべてのバッテリーの進化に貢献できると考えています。まず達成したい目先の目標は、円筒形バッテリー市場への進出ですね。
電池への投資時期は2023年から2024年がピークで、そこから1〜2年遅れてパワーデバイスに移ると思っていますので、そちらにも同時にアプローチしようと考えています。
―― 今後の展望について教えてください。
当社は設立時から4つの大きなマーケットを狙っています。1つ目が、バッテリーです。2つ目はパワーデバイス。3つ目が医療機器をはじめとする切断で、4つ目は宇宙向けデバイスです。
医療分野では、超音波メスに当社の技術を使うと、今よりさらに効率のよいものが作れることがわかっています。これは医療機器メーカーと共同開発しているところです。宇宙に関しては、ハンダのような既存の接合では難しいケースに対して、超音波による原子レベルでの接合で貢献できるのではないかと考えています。
海外展開については、韓国は、LGエナジーソリューション、サムスン電子、SKとの取引がこれから始まるところです。今後は中国マーケットへの参入、ヨーロッパのメーカーとのビジネスも視野に入れています。
EVのキーパーツであるバッテリー、パワーデバイス、モーターなどにも当社の接合技術は大きく貢献できます。安全なEV化、もしくはEVを安価にすることにおいて、当社の接合機が必要不可欠になるはずです。当社のような日本発のスタートアップが、EV化の促進に貢献できることを世界中で知ってもらえたらと思っています。
株式会社LINK-US
株式会社LINK-USは、金属の接合などに使う装置を開発する。「超音波複合振動接合」という技術を使って、材料の金属を溶かさずに接合する装置の開発と生産を手がけている。現在生産現場で一般的に使われている溶接方法は、飛散物が出たり、気泡が発生して接合強度が低くなるなどの課題がある。これらの課題を解決できるほか、溶融温度が違う金属同士を接合できるなどの特徴がある。小型化や軽量化が求められる分野の生産技術として注目されているという。 各種装置の受託販売、強力超音波応用に関するコンサルティング、超音波複合振動に関連する特許技術の供与を行っている。
- 代表者名
- 光行潤
- 設立日
- 2014年8月18日
- 住所
- 神奈川県横浜市港北区新横浜2丁目3番地4クレシェンドビル